The fascinating world of hydraulics forms an integral backbone of our modern civilization, offering its lifeblood to countless machines and infrastructures, from construction equipment and commercial vehicles to industrial machinery and domestic appliances. Yet, just like any system, it is not immune to issues, and the central player – the hydraulic hose – is particularly susceptible to an array of problems. This comprehensive exploration delves into the labyrinth of common hydraulic hose quandaries and provides you with invaluable insights into troubleshooting these issues.
Fluid Leaks
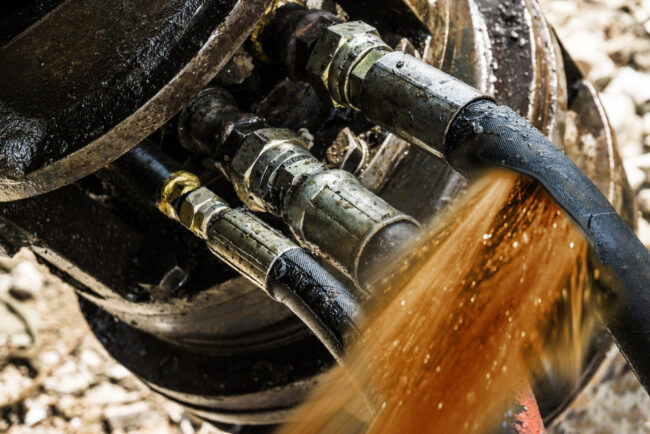
The first matter we’ll grapple with is fluid leakage, a relatively common problem that can wreak havoc on a hydraulic hose if left unchecked. Indeed, fluid leaks are notorious for their propensity to create safety hazards, reduce the efficiency of the system, and increase the cost of operation due to constant fluid replacement. Often, these leaks are a result of physical damage or deterioration, improperly installed fittings, or excessive pressure.
Hence, periodic inspection and timely intervention become essential. Look out for pools of hydraulic fluid or wet areas around the hose and fittings. Don’t ignore even minor leaks as they can rapidly escalate into major issues. If you discover a leak, isolate and depressurize the system, identify the cause, and replace the damaged components. Regularly monitor the system pressure and ensure it stays within the hose’s specified limits to prevent undue stress and subsequent leakage.
Abrasion and Wear
Let’s next turn our attention to the inevitable foe of all materials – abrasion, and wear. A hydraulic hose under constant use undergoes friction, primarily when it rubs against other parts of the system or gets exposed to rough environmental conditions. The resultant wear can compromise the hose’s structure, reducing its durability and triggering leaks.
A prudent approach involves considering abrasion-resistant hydraulic hoses during the selection process, particularly for applications with high friction. Shielding measures such as hose protectors or sleeves can also be used to curb the wear rate. Regular inspections, including checking for exposed wire or loose outer coverings, can aid in the early detection and resolution of wear-related problems.
Bursts
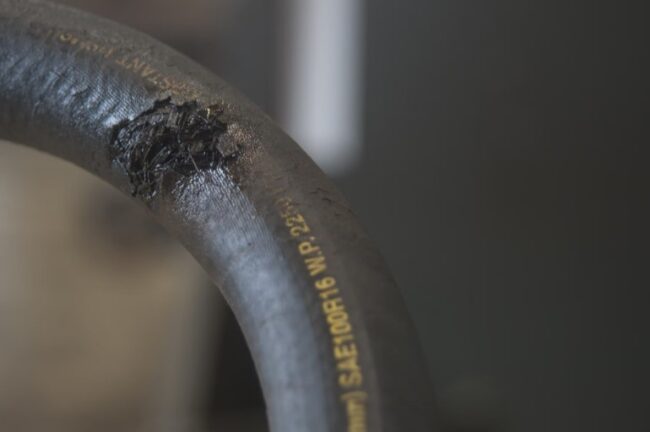
The unfortunate incident of a hose burst is as dramatic as it is destructive. Underlying reasons span from excessive pressure and hydraulic shock to the use of an improper or aged hose. A bursting hose not only disrupts system operation but poses a significant safety risk due to the abrupt release of hydraulic fluid.
Combatting bursts calls for a deep understanding of your hydraulic system and its requirements. Choosing the correct hose that can withstand the system’s maximum pressure is critical. Regular system maintenance, including checking for signs of bulging or cracks, and monitoring pressure spikes can also go a long way in preventing disastrous bursts.
Fittings and Couplings Failure
Despite being seemingly insignificant, fittings and couplings are vital cogs in hydraulic machinery. Their malfunction can stem from several reasons such as incorrect size or type, faulty installation, or simple wear and tear. When these components fail, they can lead to leaks, reduced system efficiency, or even complete system failure.
To mitigate the risk of fitting and coupling failures, make sure you use components that match your system’s specifications. Correct assembly and installation, as per the manufacturer’s guidelines, also play a crucial role in preventing failures. Remember to inspect these parts during your regular maintenance routine for any signs of damage or wear, replacing them as necessary.
Excessive Heat
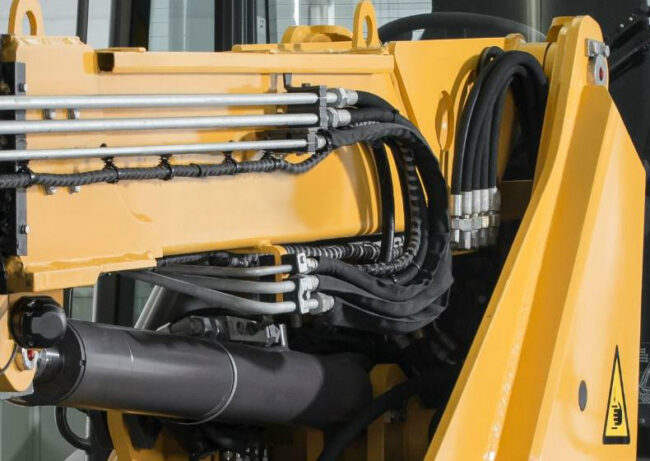
Moving onto another prevalent issue, excessive heat can prove a silent destroyer for hydraulic hoses. High temperatures can degrade the hose materials, reduce their flexibility, and lead to cracks or leaks. Causes of overheating include environmental conditions, high fluid temperatures, or lack of adequate cooling mechanisms.
In the quest to battle excessive heat, consider hoses designed to withstand high temperatures. Employ heat shields or heat-resistant sleeves, particularly in hot environments or applications where the hose is close to hot components. Ensure your hydraulic system has an efficient cooling mechanism and monitor the fluid temperature to prevent it from reaching harmful levels.
Contamination and Impurities
Our journey into common hydraulic hose problems wouldn’t be complete without discussing contamination and impurities. Foreign substances entering the hydraulic fluid can cause blockages, wear down system components, and lower overall efficiency. These can enter the system during maintenance, through worn seals, or via contaminated fluid replacements.
The remedy to contamination lies in a rigorous, cleanliness-focused protocol. Use clean, filtered hydraulic fluid for replacements. Properly seal the system to prevent the ingress of foreign materials. Regularly check and clean or replace filters to maintain a clean hydraulic environment. For problematic contamination issues, fluid analysis might be necessary to identify and tackle the contaminants.
Hose Assembly Installation Issues
Often overlooked yet crucial, hose assembly installation issues can result in a multitude of problems, from leaks and kinks to premature failure. Common installation missteps include incorrect length, improper routing, or excessive bending.
To sidestep such pitfalls, always follow the manufacturer’s instructions when installing a hose assembly. Ensure the hose length allows for changes in system dimensions due to thermal expansion or machine movement. Route the hoses to avoid sharp bends, twists, or contact with moving parts. Employ proper support clamps and protective sleeves to maintain the hose in its optimal position and condition.
Aging and Degradation
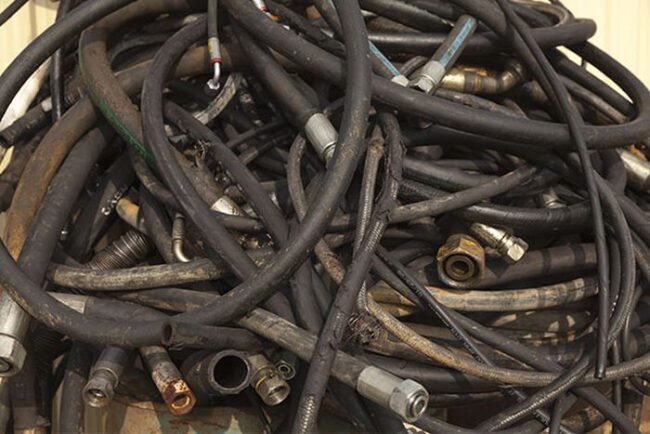
Lastly, let’s delve into a phenomenon that even hydraulic hoses can’t evade – aging. Over time, hoses may degrade due to environmental factors, constant stress, or simple wear and tear. Aging hoses may exhibit brittleness, cracks, or reduced performance, ultimately leading to failure.
As we tackle aging, remember that prevention is always better than cure. Implement a regular replacement schedule based on the hose’s expected lifespan and operating conditions. Conduct regular inspections for signs of aging and degradation, replacing hoses proactively rather than waiting for failure to occur.
Final Thoughts
The intricate dance of hydraulics is a marvel of modern engineering, yet it is not without its potential pitfalls. As we’ve journeyed through the labyrinth of common hydraulic hose issues, it’s evident that regular inspections, appropriate selection of components, proper installation, and timely intervention are the cornerstones of maintaining a healthy hydraulic system. By understanding these problems and their solutions, you can ensure the smooth operation of your hydraulic systems, contributing to safer workplaces, efficient operations, and ultimately, a more sustainable world.